Factory Manager Job Description
factory manager job description includes a detailed overview of the key requirements, duties, responsibilities, and skills for this role.
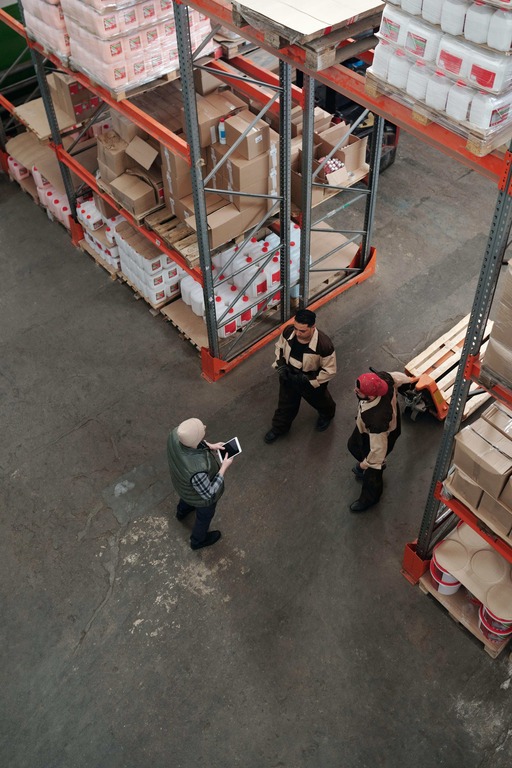
Factory Manager Job Description
A factory manager oversees the physical operation of a factory.
A factory manager may oversee one facility or hundreds of facilities.
A factory manager may also oversee a division or a workshop within a factory.
A factory manager is often responsible for hiring, training, and supervising employees, allocating work hours, and controlling budgets.
A factory manager’s work responsibilities frequently include estimating manufacturing costs, developing production schedules, and ensuring that quality control standards are met.
Job Brief:
We’re looking for a Factory Manager to lead our team of production workers. You will be responsible for overseeing the day-to-day operations of the factory, including supervising employees, monitoring production, and enforcing safety regulations. In addition, you will need to ensure that the factory is running efficiently and meeting production targets. If you are a motivated leader with experience in manufacturing, then we want to hear from you!
Factory Manager Duties:
- Manage and lead all facility, production, and administrative departments
- Ensure that the facility runs efficiently with the highest productivity possible
- Ensure that each department is producing products of the highest possible quality
- Conduct periodic inspections of all departments to ensure standards are met
- Maintain constant communication with employees, suppliers, and vendors
- Keep up to date on all current events and issues in the manufacturing industry
- Oversee safety protocols and programs
- Ensure that all employees and subcontractors are following all safety protocols
Factory Manager Responsibilities:
- Train, motivate, and supervise factory operations while adhering to all safety, performance, and environmental standards
- Ensure production and safety goals are achieved
- Direct and ensure all production, quality control, and quality assurance processes are implemented to promote productivity, product quality, and company reputation
- Manage and motivate employees to ensure job is accomplished efficiently
- Oversee all production decisions, including production and quality control-related staffing, scheduling, and materials
- Conduct facility and equipment audits, and inspect product and process quality
- Provide training, and gather metrics on training effectiveness to ensure training of all staff
- Make regular trips to factory to oversee production, track performance, and solve problems
- Maintain electronic records of all material, production, inventory, and labor to ensure cost efficiency and regulatory compliance
- Manage and supervise all warehouse and shipping operations
- Communicate with overseas vendors
Requirements And Skills:
- Bachelor’s degree or 5+ years experience in engineering and operations management
- Experience in design and development of new manufacturing processes
- Strong leadership and team building skills
- Knowledge of manufacturing, industrial, and safety standards and procedures
- Proven ability to manage multiple projects simultaneously with a constant eye on quality
At [Company Name], we celebrate diversity and are committed to building an inclusive team. We encourage applications from people of all races, religions, national origins, genders and ages, as well as veterans and individuals with disabilities.