Industrial Engineer Job Description
industrial engineer job description includes a detailed overview of the key requirements, duties, responsibilities, and skills for this role.
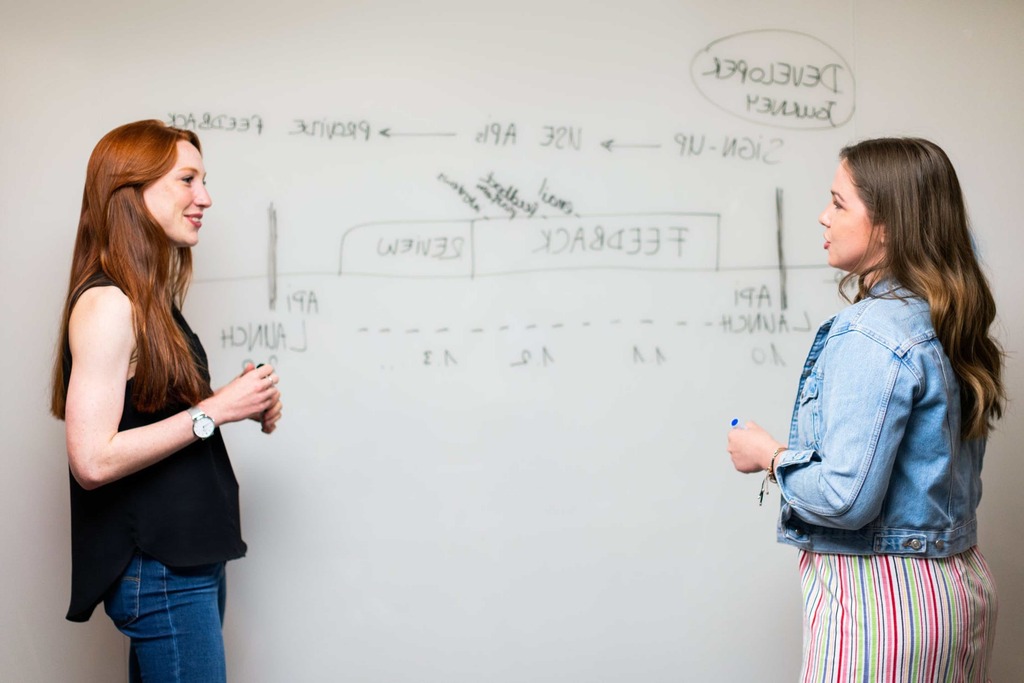
Industrial Engineer Job Description
An industrial engineer is an engineer who studies human interaction in complex systems, and the optimization of individual and system performance.
An industrial engineer is employed by an organization or company to help identify, create, and improve systems within an organization.
The individual usually works within a manufacturing or processing environment, and develops strategies and systems to improve production or efficiency.
An industrial engineer usually has a bachelor’s or master’s degree in engineering.
Job Brief:
We’re looking for an Industrial Engineer who can help us to improve our manufacturing process. The ideal candidate will have experience in Lean Manufacturing and Six Sigma.
Industrial Engineer Duties:
- Research and study ways to maximize the efficiency of production, manufacturing, industrial, and manufacturing processes using both new and existing technology
- Maintain current knowledge of all proposed changes and developments in manufacturing and production, as well as the industry
- Develop and plan manufacturing strategies, procedures, and policies
- Assesses existing materials and equipment to determine their quality and possible improvements
- Maintain accurate records and reports of current operations
- Implements, maintains, and improves manufacturing, industrial, or manufacturing processes
- Researches new materials and production methods
- Coordinate work processes to meet projected deadlines and objectives
- Supervise and coordinate activities of manufacturing, industrial, or manufacturing processes
- Schedule and allocate resources, including people, budgets, and time
- Align manufacturing, industrial, or manufacturing processes with company strategy
- Keep abreast of trends in industrial engineering
- Meet production goals
Industrial Engineer Responsibilities:
- Performs a variety duties to assist in planning, organizing, directing, coordinating, and evaluating work activities, including monitoring productivity, production, and inventory levels
- Maintain project timelines, and assure that tasks are accomplished on time
- Develop, implement, and maintain budgetary and resource allocation plans
- Delegate responsibilities to the best employees to perform them while enforcing all policies, procedures, standards, specifications, guidelines, training programs, and cultural values
- Resolve internal staff conflicts efficiently and to the mutual benefit of those involved
Requirements And Skills:
- Bachelor’s degree in engineering, business, or related field
- 2+ years experience in support of manufacturing or industrial operations
- Strong knowledge of manufacturing processes and technologies, including statistical methods and control
- Strong problem solving and decision making abilities
- Knowledge of industrial systems and equipment
- Strong communication skills
At [Company Name], we believe that diversity and inclusion are essential to building a successful team. We are committed to providing equal opportunity for all employees and encourage applications from people of all races, religions, national origins, genders, and ages, as well as veterans and individuals with disabilities.